“That is exactly why we recently announced a rapid fabrication facility for Europe in Telford in the UK which allows us to say to the market currently investigating 3D printing technologies for plastics ‘look, you don’t have to invest in the technology in-house yourself, you can still benefit with a manufacturing partner such as Ricoh.’”
Rising demand
According to Philip Brady, country manager for Canon, the figures Gartner is putting out are highly encouraging, with end-user spending on 3D printers predicted to increase from $1.6 billion (€1.4 billion) in 2015 to around $13.4 billion (€12 billion) in 2018.
“We see this as particularly of interest. This year we entered into a distribution agreement with 3D Systems, a leading provider of 3D printing technology and under the arrangement, we will market, sell and support its advanced manufacturing 3D printers in the UK and Ireland, with a view to rolling out across Europe,” he said.
“Customers will have access to 3D Systems’ advanced 3D printing technology underpinned by our service and support.”

The start-up investment for an injection mould is anywhere from €10,000 to €50,000 and that is a huge barrier for small companies entering markets. If you do spend that money then you’re still limited in what can make because you can’t easily make changes. Effectively once the mould is set you’re stuck with it unless you want to spend the same money again on a new one. But with a 3D printing set up, things are infinitely more versatile, Debra Laefer, U3D
According to Brady, this partnership reflects Canon’s ongoing growth strategy of expansion into new technology domains and builds on a similar agreement it entered into with 3D Systems in Japan last year.
“The goal is to offer the means to prototype for rapid product development, with a focus on our engineering, manufacturing and architectural customers. In particular we think that plug and print capability will drive market growth this year,” he said.
While the ecosystem remains complex, plug and print printers use locked-in materials available in vendor-specific cartridges as with 2D printers to maximise the likelihood the materials will work well.
“Automated bed levelling and heated build chambers also facilitate simpler set-up and operation, making it easier for the consumer to just ‘hit print’ and successfully produce a 3D item. Outside of prototyping, we’re seeing architects using the technology for client and concept models in addition to full model printing while we’ve also seen universities using the technology for fashion, fine art, jewellery, medical, chemistry and physics-related purposes.”
Industry partnerships
Meanwhile, elsewhere in the country a number of interesting partnerships between universities and private businesses are producing new entities able to work with enterprises looking to dip their toe in 3D print waters.
U3D is around a year old, operating as the first fully commercial 3D printing hub in Ireland. As well as conventional low end 3D printers, it has two metal printers and two high end plastics printers that can print down to a resolution of 15 microns, or half the width of a human hair. It offers training and print services to Irish companies looking for the advantages that working with 3D printing can offer.
“The cliché is that 3D printing gets used for prototyping and novelty projects, and that’s not entirely incorrect but it’s very far from the full picture,” said Debra Laefer, centre director for U3D and civil engineering expert.
“Metal printers are currently being used to print automobile and plane parts, dental implants, titanium hip implants for the biomedical sector and really anywhere there is a requirement for highly specialised products.”
According to Laefer, the current generation of printers and material suppliers cannot financially compete with injection moulding, once the items being printed go above a certain number of units. But at lower levels, it’s extremely competitively priced.
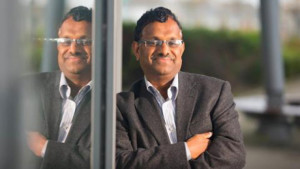
Our build plate is currently 28 x 28cm, so if you if you are building a product that’s 10cm tall, you can fit five this way and five that way and so print 25 different designs at the same time. You can find the best and then go and manufacture that. That level of iteration would be extraordinarily expensive to do by conventional means. It would take a lot of time, money and difficulty to do that,” Dr Ramesh Raghavendra, SEAM
Start-up cost
“The start-up investment for an injection mold is anywhere from €10,000 to €50,000 and that is a huge barrier for small companies entering markets. If you do spend that money then you’re still limited in what can make because you can’t easily make changes. Effectively once the mould is set you’re stuck with it unless you want to spend the same money again on a new one. But with a 3D printing set up, things are infinitely more versatile,” she said.
“If you decide you’ve got something wrong with your product or that you’ve misread the market you can change your product immediately.”
This is something that Dr Ramesh Raghavendra of the South Eastern Applied Materials (SEAM) Research Centre agrees.
Subscribers 0
Fans 0
Followers 0
Followers